You Define Success. We Help You Achieve It.
We listen because we want to understand your situation, challenges, and objectives. Our process is designed to help you evaluate the economic, production, and environmental benefits of operational strategies, maintenance practices, efficiency gains, optimization of current equipment, and capital upgrades. We will help you identify and manage the intent throughout the process, meaning you are able to realize the results that you need through the most cost-effective methods.
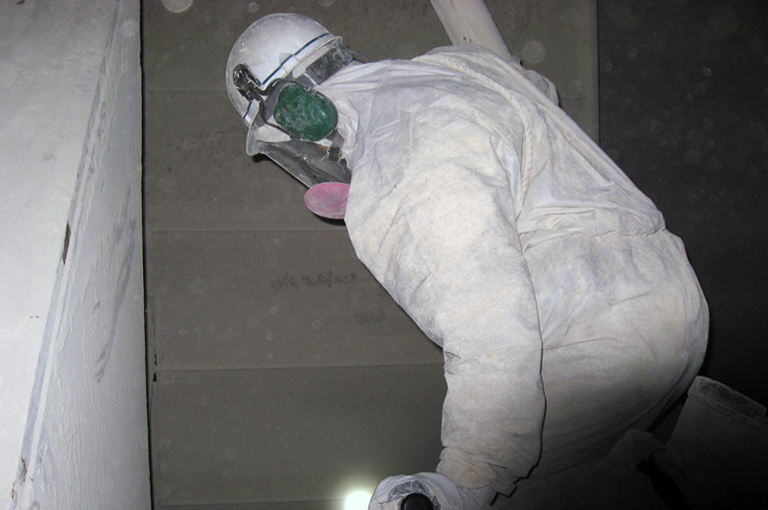
Achieving Sustained Compliance in Waste-to-Energy Facility
Poor ESP performance created challenges for maintaining consistent emissions compliance. Since the repairs needed were extensive, and shutdown time would not allow for all work to be completed, a phased plan was put in place. The results were consistent compliance, sustained over time.
Read More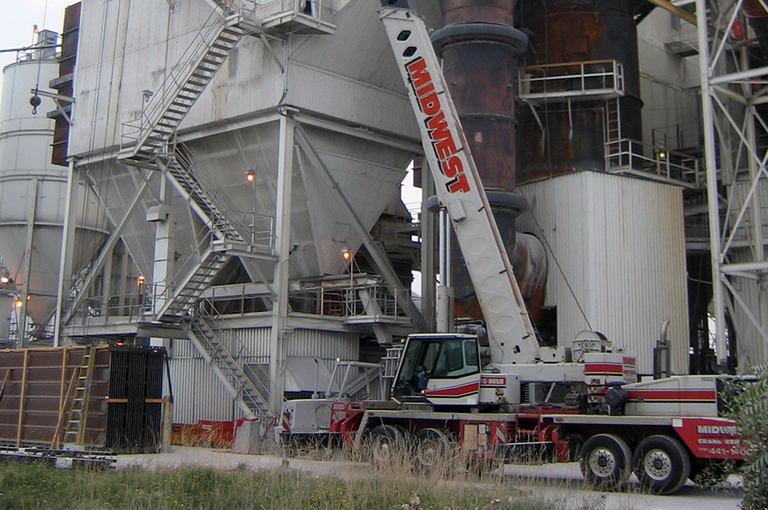
Analysis, Optimized Maintenance Spending, Renewed Performance
Despite consistent maintenance and operational efforts, the precipitator's performance was limiting load. Neundorfer completed an operational review and inspection, putting together a prioritized plan that allowed the plant to optimize the maintenance spend for the next outage. And they got the performance back.
Read More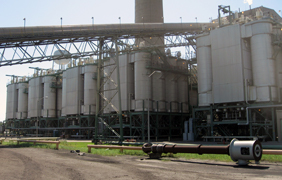
Baghouse Integration Dramatically Reduces O&M Costs
A 1,500 MW Southeastern U.S. coal-fired power plant was able to improve the effectiveness of their fly ash evacuation systems and reduce the costs of operation and maintenance by an expected 50% through improved, integrated instrumentation.
Read More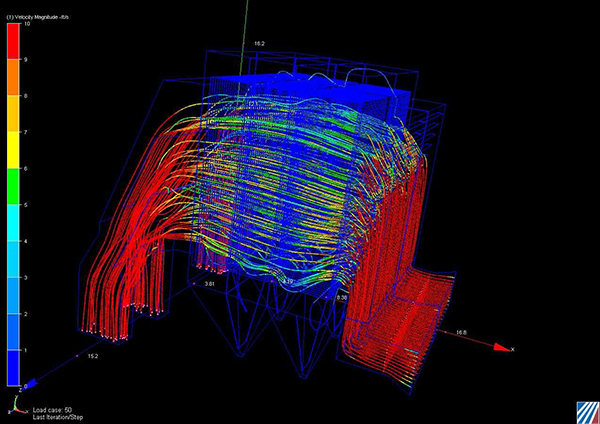
Cement Plant Gains Consistent Operations
A Midwestern cement plant needed to balance cost, outage time, and performance gains in order to make the best use of short outages to address the weak links in the air pollution control equipment. The result was a plan for incremental projects that would achieve the greatest performance and reliability gains with the lowest overall capital investment.
Read More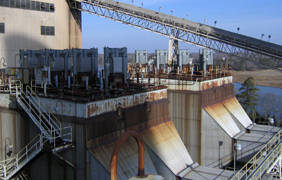
Creative Approach, Thoughtful Analysis Saves Two Coal Plants
When the plant's initial assessment indicated MATS compliance would require high-cost upgrades, the future of two plants was uncertain. By modeling improvements over the entire process, Neundorfer identified a low-cost compliance program that would ensure these plants continue to meet their operational goals long into the future.
Read More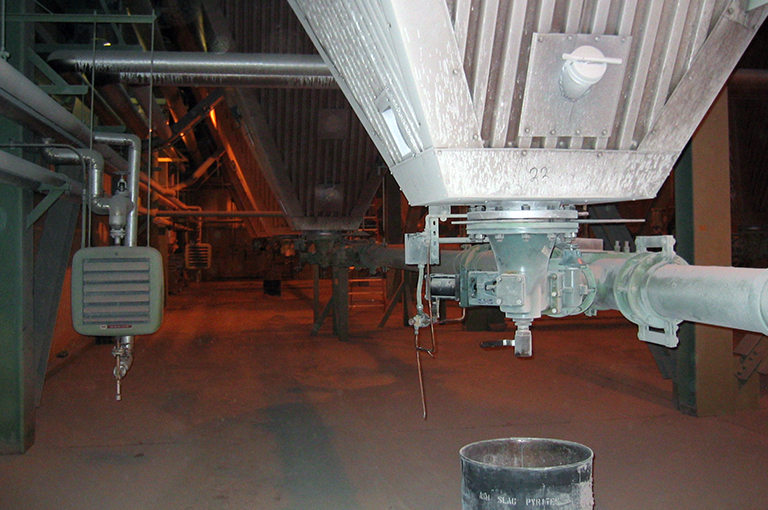
Focus on Operational Flexibility Reduced Derates, Improves Capacity
As the hopper evacuation system struggled to keep up with the collection profile of the unit, nightly derates were required to maintain operations. With improve performance and ash collection profiles, the plant was able to increase capacity, run consistently at high load, and save on maintenance costs.
Read More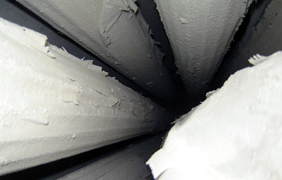
Holistic Troubleshooting Helps Resolve Baghouse Cleaning Issues
The most obvious fix turned out not to be the best one when Neundorfer helped a utility resolve baghouse cleaning issues that were limiting its ability to run at full load. Use of a multi-phase planning process and holistic troubleshooting approach yielded an innovative solution that exceeded expectations.
Read More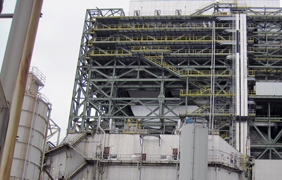
Justifying Controls with Opacity-Driven Energy Optimization
At a paper mill in New England, a long-delayed controls upgrade project was cost-justified within eight months of completion. The improved performance and energy savings from an ESP controls project saved the mill an average of $8,000 per month.
Read More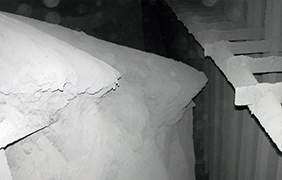
Keys to Sustained Performance Improvements
A Midwestern utility had a problem: precipitator performance was sub-par, resulting in reduced power generation and undesirable opacity levels. Called in as a consultant, Neundorfer helped the utility identify causes and fix the problem through internal ESP modifications and upgrades to the flue gas conditioning and hopper evacuation systems.
Read More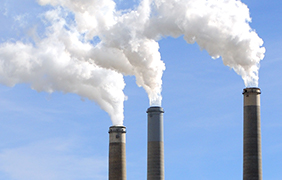
Low Emitter Status Achieved with Low-Cost Effort
A Midwest power plant called on Neundorfer to use its analytical skills, field experience and modeling capabilities to provide a low-cost/high-value solution that will allow them to achieve LEE (Low Emissions Emitter) status while forgoing the need for expensive monitoring equipment and a quarterly testing protocol.
Read More
Maintaining Operations after Equipment Damage
When an industrial steam generator experienced a major process upset and damaged their electrostatic precipitator (ESP), they could not shut down to make the necessary repairs. Neundorfer was able to optimize the performance of the precipitator which allowed the plant to find the production point that would allow the equipment to stay in compliance until the regularly scheduled shutdown.
Read More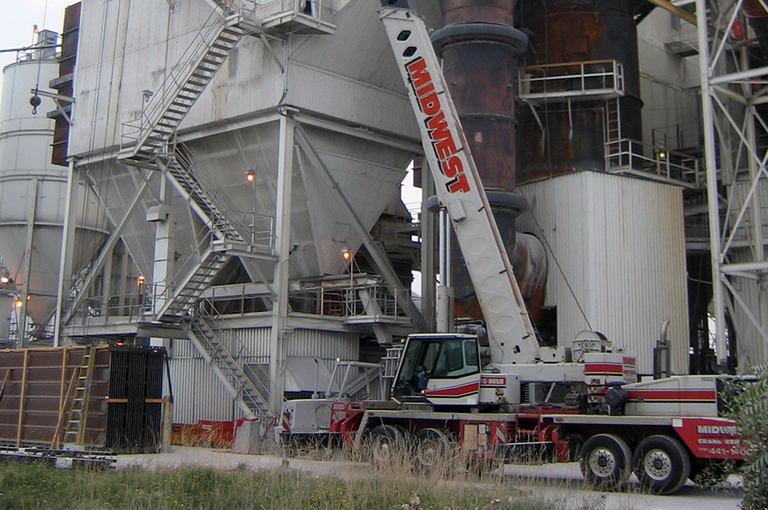
Meeting NESHAP Rules Through Collaboration and Analysis
Recently a cement plant customer was able to celebrate a huge "win" as a result of a collaborative strategy with Neundorfer. Following implementation, emissions levels tested at 70% below the new limit, filling the customer with a new-found confidence in their operations and helping them meet new NESHAP rules.
Read More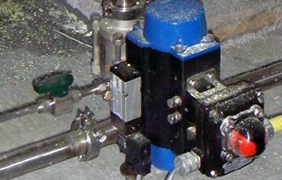
Optimizing SO3 Systems in Multiple-Unit Plants
Installing separate SO3 flue gas conditioning systems on two units at Duke Energy's Beckjord Power Plant fixed ongoing struggles to maintain acceptable stack emission levels. Neundorfer provided one of the SO3 systems, and helped Duke Energy save money by refurbishing a system for the other unit.
Read More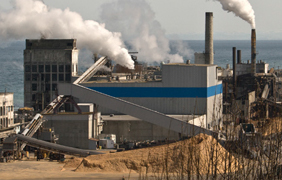
Paper Mill Gains Operational Flexibility While Reducing Emissions
A paper company in Wisconsin was contemplating expensive precipitator modifications to reduce emission levels. Through modeling we discovered the same result could be achieved for much, much less by making relatively simple gas flow distribution changes.
Read More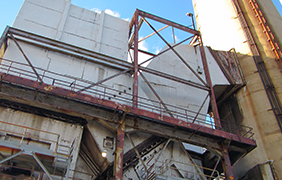
Reliable, More Effective Granular Sulfur Feeder
When Duke Energy's Allen Steam Station started upgrades to the granular sulfur feed system for three of its units, the utility partnered with Neundorfer to reduce emissions and improve reliability.
Read More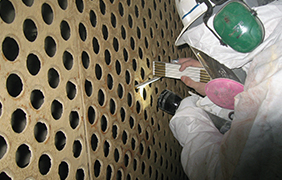
Results-Driven Decisions, Remarkable Results
When a metal processing plant experienced a major interruption, Neundorfer's team pulled out all the stops to assess the situation, perform a thorough analysis, and create an action plan that would get the plant back on line in only a few days while improving the reliability and performance of the unit.
Read More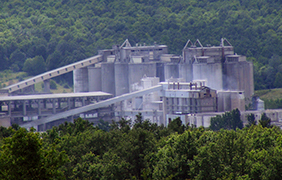
Rising from the Ashes
Following a kiln outage in early 1997, a fire destroyed four precipitators at Holnam Cement in Clarksville, Missouri. Within two days, Neundorfer and Holnam had a plan for replacing ESP components. Eighteen weeks after the fire, the rebuild was complete.
Read More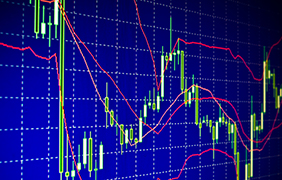
Smart Use of Data Improves Diagnostics, Optimizes Performance
Chronic operating issues and costly technical support was plaguing a southern paper mill. There had to be a better way. By analyzing data and using modeling to generate insights into performance-based maintenance and operational strategies, Neundorfer engineers were able to identify effective resolutions without leaving the office.
Read More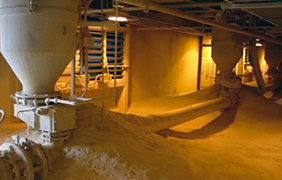
SmartAsh Case Study
A large power generation plant needed to improve its fly ash evacuation system and turned to Neundorfer. The system, serving 20 hoppers on three separate precipitators, was upgraded without requiring an outage.
Read More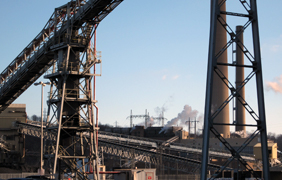
Upgrading Precipitator Controls Quickly Improves Performance
Neundorfer helped Reliant Energy's Cheswick station improve consistency and overall precipitator performance by installing upgraded controls and Precipitator Optimization System (POS) software.
Read More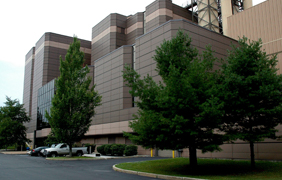
Waste-to-Energy Upgrades Yield Dramatic Improvements
When Ecomaine replaced precipitator power controls and rapping controls with new technology from Neundorfer, the intent was to ensure consistent compliance with heavy-metal emission limits, and hopefully save some energy. After installation, the plant was able to get significantly more power into the ESP, and far exceeded its goals of improving collection efficiency.
Read More